n8n Workflow for Quality Control Alerts
Create real-time SMS alerts when defects exceed thresholds.
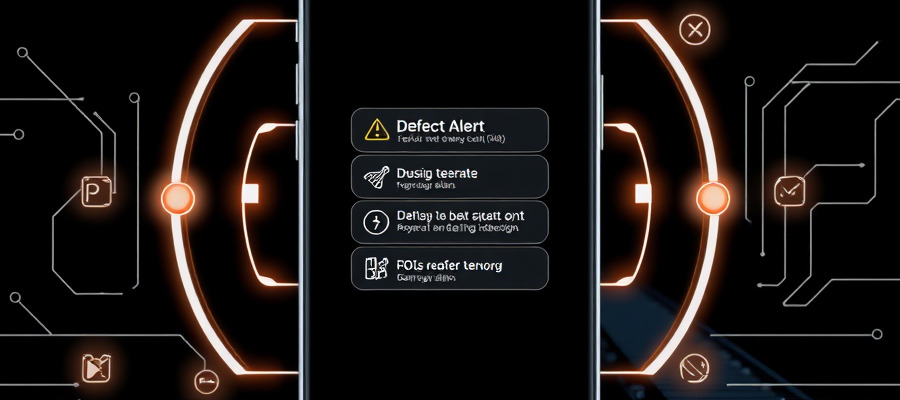
Automate Quality Control Alerts with n8n: A Step-by-Step Guide
Quality control automation is transforming how businesses monitor production processes. By integrating real-time alerts and error tracking, teams can respond faster to defects, reduce waste, and maintain compliance. This guide shows how to build a no-code quality control automation system using n8n, a flexible workflow automation platform.
Why Use n8n for Quality Control Automation?
n8n simplifies connecting data sources, triggering alerts, and integrating with communication tools like SMS. Key benefits include:
- Real-Time Monitoring: Detect defects the moment they exceed pre-set thresholds.
- Cost Efficiency: Reduce manual inspections and human error.
- Scalability: Adapt workflows as production demands change.
- Multi-Channel Alerts: Notify teams via SMS, email, or Slack.
How to Build a Quality Control Alert Workflow in n8n
Here’s how to automate defect alerts using n8n’s visual workflow builder:
Step 1: Connect Quality Data Sources
- Integrate IoT Sensors or Databases: Use n8n nodes like MQTT or PostgreSQL to pull defect counts from production line sensors or ERP systems.
- Set Thresholds: Define acceptable defect rates (e.g., “Alert if >5% defects in 1 hour”).
Step 2: Trigger Conditional Alerts
- Compare Values: Use the IF node to check if defect rates exceed thresholds.
- Filter Noise: Ignore minor spikes with delay nodes or rolling averages.
Step 3: Send Real-Time SMS Alerts
- Integrate SMS Services: Connect providers like Twilio or Plivo to notify quality managers instantly.
- Customize Messages: Include defect metrics, timestamps, and production line IDs.
Real-World Applications
- Manufacturing: Flag machine errors before they lead to batch failures.
- Food Production: Monitor hygiene or temperature compliance.
- E-Commerce: Alert teams about defective products in fulfillment centers.
Benefits of Automating Quality Control
- Faster Response: Resolve issues before they escalate.
- Data-Driven Decisions: Use historical data to identify recurring problems.
- Compliance: Automatically log incidents for audits.
Get Started with Custom Quality Automation
Ready to implement quality control automation for your business? Our team builds tailored workflows using n8n, Zapier, and custom tools to streamline your operations.